전기차 배터리팩 설계 방식 완전 정복: 셀투팩, 셀투바디, 모듈 방식의 차이점과 실제 적용 사례
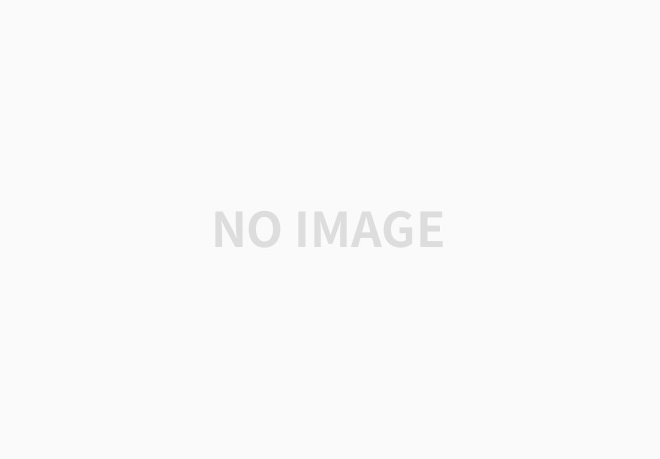
전기차의 심장이라 할 수 있는 배터리팩은 차량의 주행 성능, 안정성, 공간 활용, 그리고 유지보수에 이르기까지 다양한 요소에 직접적인 영향을 줍니다. 특히 배터리팩을 어떻게 설계하느냐에 따라 효율성과 성능은 천차만별로 달라지죠. 이번 글에서는 전기차 배터리팩의 대표적인 설계 방식인 **모듈 방식(Modular Pack), 셀투팩(Cell-to-Pack, CTP), 셀투바디(Cell-to-Body, CTB)**에 대해 각각의 구조적 특징과 장단점, 그리고 실제 적용된 전기차 모델 사례를 바탕으로 자세히 알아보겠습니다.
1. 모듈 방식 배터리팩: 전통적인 구조, 검증된 안정성
모듈 방식은 가장 오랫동안 사용되어 온 전통적인 배터리팩 설계입니다. 이 방식은 먼저 배터리 셀을 소단위로 묶어 **배터리 모듈(Battery Module)**을 만들고, 이러한 모듈을 여러 개 결합해 하나의 **배터리팩(Battery Pack)**을 구성하는 방식입니다.
이 구조의 가장 큰 장점은 안정성과 유지보수의 용이성입니다. 예를 들어 모듈 중 일부에서 문제가 생겼을 경우, 전체 배터리를 교체하지 않고 해당 모듈만 분리하여 교체할 수 있어 효율적입니다. 또한 모듈 단위로 방열 시스템을 설계할 수 있어 열 분산이 용이하고, 차량의 화재나 폭발 위험도 상대적으로 낮습니다.
하지만 단점도 존재합니다. 모듈 단위로 구조물을 추가하다 보니 배터리 셀이 차지하는 공간 대비 실제 에너지 저장 공간이 줄어들고, 전체적인 무게도 증가하게 됩니다. 이는 곧 공간 효율성 저하와 주행거리 손실로 이어집니다.
대표적인 적용 사례로는 테슬라 모델 S와 모델 X, 그리고 현대 아이오닉 5 등이 있습니다. 특히 현대의 E-GMP 플랫폼은 모듈 방식을 기반으로 하면서도 안정성과 공간 활용을 모두 고려한 고효율 설계를 자랑합니다.
2. 셀투팩(Cell-to-Pack, CTP): 모듈을 없애고 효율을 높이다
셀투팩 방식은 전통적인 모듈 구조를 과감히 생략한 차세대 배터리팩 설계 방식입니다. 배터리 셀을 직접 배터리팩에 조립함으로써 모듈 구조 없이 배터리 밀도를 극대화할 수 있습니다.
가장 큰 장점은 에너지 밀도 향상입니다. 같은 공간에 더 많은 셀을 집어넣을 수 있어, 차량의 주행거리를 증가시킬 수 있습니다. 또한 모듈 구조를 생략함으로써 생산 공정을 간소화할 수 있고, 결과적으로 제조 비용도 절감됩니다. 구조적으로도 불필요한 부품이 제거되기 때문에 차량 무게가 줄어들고, 효율성은 증가합니다.
단점으로는 셀 간의 열관리 문제와 충격 시 보호 성능이 상대적으로 떨어질 수 있다는 점이 있습니다. 또한 셀 개별 교체가 어렵기 때문에 유지보수 시 전체 팩을 교체해야 할 수도 있습니다.
대표적인 적용 사례로는 중국 BYD의 블레이드 배터리가 있습니다. 이 배터리는 길고 얇은 셀을 사용하여 CTP 구조로 구현되었고, 열안정성이 뛰어나 높은 안전성을 확보했습니다. 또 하나의 예시는 테슬라 모델 Y로, CATL의 LFP(리튬인산철) 기반 CTP 배터리를 채택해 비용 효율성과 공간 활용을 모두 만족시켰습니다.
3. 셀투바디(Cell-to-Body, CTB): 배터리가 차체가 되다
셀투바디는 가장 혁신적인 설계 방식으로, 배터리팩을 차량 차체의 일부로 통합하는 구조입니다. 즉, 배터리팩이 단순한 에너지 저장 장치가 아니라, 차량 섀시(Chassis)의 구조적 기능까지 수행하게 됩니다.
이 방식의 가장 큰 장점은 공간 활용성과 구조적 강성의 획기적 향상입니다. 기존에는 배터리팩을 차량 하부에 탑재하고 별도의 프레임으로 고정해야 했지만, CTB는 차체 자체에 셀을 삽입하므로 별도의 공간이 필요 없습니다. 이로 인해 더 많은 배터리를 탑재할 수 있고, 차량 하부 구조의 강성도 높아져 충돌 안전성도 향상됩니다. 또한 구조 통합 덕분에 차량의 무게를 더욱 줄일 수 있는 여지도 큽니다.
하지만 단점도 명확합니다. 가장 큰 단점은 사고 발생 시 수리 비용이 매우 높고, 복구가 어렵다는 점입니다. 차량 충돌 시 배터리와 차체가 함께 손상될 가능성이 크기 때문에, 단순한 배터리 교체만으로 문제가 해결되지 않을 수 있습니다.
이 구조는 테슬라 모델 Y와 테슬라 사이버트럭에 적용되었습니다. 특히 테슬라의 구조적 배터리팩은 차량의 하부를 지지하는 프레임 역할까지 수행하며, CTB 기술을 바탕으로 무게를 줄이고 주행거리와 강성을 동시에 확보했습니다.
4. 미래 배터리팩 설계의 방향은?
현재 자동차 업계는 배터리 설계 방식을 점차 모듈 방식에서 CTP, 그리고 CTB로 진화시키고 있습니다. 각 단계마다 주행거리 향상, 공간 효율성 증가, 생산 비용 절감, 차량 경량화라는 명확한 목표가 있으며, 이 기술의 발전은 곧 전기차의 성능 향상으로 이어집니다.
앞으로는 CTP와 CTB 방식이 대세로 자리 잡을 가능성이 높습니다. 특히 CTB는 자율주행과 고속 주행, 차량 경량화가 중요한 미래차 시장에서 핵심 기술로 주목받고 있으며, 많은 글로벌 완성차 업체들이 이 기술을 도입하기 위한 개발을 진행 중입니다.
5. 결론
안정성과 유지보수를 중요시한다면 모듈 방식이 유리합니다.
공간 활용과 에너지 밀도를 중시한다면 CTP 방식이 적합합니다.
차체 경량화와 구조 강화, 미래 지향적 설계를 원한다면 CTB 방식이 최선입니다.
전기차 배터리팩은 단순한 부품이 아니라, 전기차 전체 성능을 좌우하는 핵심 기술입니다. 각 설계 방식의 특징과 실제 적용 사례를 이해하면, 향후 전기차 선택 시 좀 더 똑똑한 소비자가 될 수 있습니다.
'자동차 관련 기술' 카테고리의 다른 글
커넥티드카 정의 종류 특징 법규 자동차 적용 사례 Connected Car V2X OTA (16) | 2025.04.09 |
---|---|
매트랩 시뮬링크 툴의 종류, 특징 및 장단점, 용도, 자동차 산업 적용 사례 simulink simscape Matlab (14) | 2025.04.08 |
2025 서울 모빌리티쇼 모터쇼 참가 기업, 신차, 신기술 총정리 전기차 (8) | 2025.04.06 |
자동차 자율주행 Autonomous Driving 기술 SAE 레벨, 법규, 특징 및 최신 개발 동향 (16) | 2025.04.03 |
자동차 기능안전 Functional Safety 정의, 등급, 법규, 적용 사례 ISO26262 ASIL (13) | 2025.04.02 |